在原油開采與煉化領域,含水率超標的原油不僅增加運輸成本,還易引發管道腐蝕與煉化設備故障。
高頻變頻原油脫水試驗儀通過模擬工業電場環境,成為實驗室與現場優化脫水工藝的核心設備。其以高頻脈沖電場(500Hz-20kHz)為技術核心,可在30分鐘內將原油含水率從80%降至5%以下,為油田提質增效提供關鍵數據支撐。
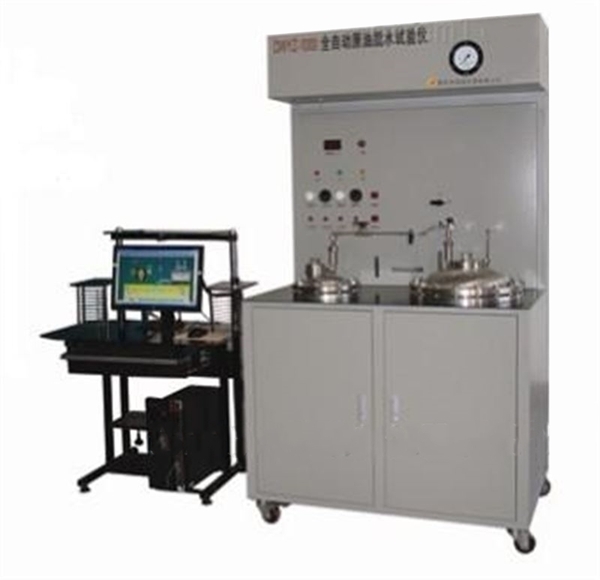
1.技術內核:變頻電場與智能調控
高頻變頻原油脫水試驗儀的核心在于其動態電場調控技術。設備采用雙極性高頻脈沖電源,輸出電壓范圍覆蓋0-50kV,頻率可在500Hz至20kHz間連續可調。例如,某國產機型通過IGBT逆變模塊與DSP控制系統,實現電場強度(0-10kV/cm)與脈沖寬度(1-100μs)的獨立調節,以適應不同黏度原油(5-500mPa·s)的脫水需求。在智能控制方面,設備內置PID算法,可自動補償原油電導率變化(0.1-1000μS/cm),確保脫水效率穩定。例如,在處理高含蠟原油時,系統通過高頻振動(15kHz)抑制蠟晶沉積,使脫水率較傳統工頻電場提升25%。
2.場景賦能:從實驗室到油田現場
在科研領域,試驗儀可驗證新型破乳劑的協同效應。例如,某高校團隊通過該設備發現,將納米二氧化硅與聚醚型破乳劑復配后,在12kHz電場下可將脫水時間縮短40%,且油水界面清晰度提升3個等級。油田現場則更關注工藝參數優化,例如大慶油田采用移動式試驗車,在井場實時調整電場頻率(8-18kHz)與溫度(40-70℃),使聯合站脫水成本降低0.8元/噸。針對海上平臺空間限制,緊湊型設備通過集成油水界面傳感器,實現脫水后污水含油量(≤100ppm)的閉環控制,較重力沉降法效率提升10倍。
3.未來演進:綠色化與智能化融合
隨著“雙碳”目標推進,試驗儀正加速向低能耗與智能化轉型。新一代設備采用碳化硅(SiC)功率器件,使電能轉換效率提升至95%,較傳統硅基器件節能20%。例如,某機型通過余熱回收系統,將電場發熱量用于原油預熱,綜合能耗降低35%。智能化方面,設備搭載機器學習模型,可基于原油物性數據庫(含10萬+組數據)自動推薦較優電場參數,預測脫水效果誤差小于5%。此外,5G通信模塊支持遠程調試與故障診斷,使偏遠油井的脫水工藝優化響應時間縮短至2小時。
從實驗室到油田深處,高頻變頻原油脫水試驗儀正重塑原油提質的技術路徑。其不僅推動著破乳劑研發與電場參數設計的范式革新,更為老油田穩產、稠油開發等難題提供解決方案。隨著國產設備在耐高壓絕緣材料、高頻電源技術上的突破,這一“電場杠桿”正撬動萬億級原油加工產業的綠色升級。